Heres some shrinkage bars of various porcelains Sasuga and MC porcelain which at one time I had made for me in a slip business. Several factors including firing time and temperature can vary slightly per kiln which can impact the actual shrinkage.
Different bodies exhibit differing drying shrinkage curves.
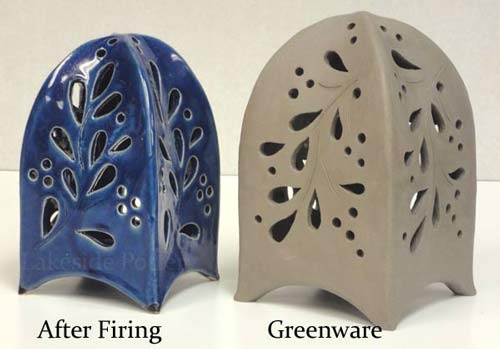
Why the saiz is change when making shrinkage in ceramic. For example earthenware pots tend to shrink between 6-8 when fired to cone 6. With the increase of sintering temperatures the foam shrunk increasingly. Beth Peterson is a pottery expert sharing her knowledge about producing pottery on the wheel as well as handbuilt ceramic sculpture and the Raku firing technique of pottery making.
Once you have mixed up a batch of clay do a. When the design of the gating system contradicts the solidification principle of the casting. When the sintering temperature was up to 1500 C the shrinkage increased slowly.
The glaze on ceramic sinks ensures a very smooth seamless finish which prevents lime scale and dirt from attaching itself making them easy to keep clean. Beth has over 30 years of experience crafting with clay. Select Channels Clay Making Channel Studio Tips Ceramic Sculpture Glaze Making Channel Raw Materials Channel Places Channel Finishing Techniques Channel Glazing Techniques Channel Architectural Ceramics Channel Production Channel Time Capsule.
To change your display in Windows 10 select Start Settings Ease of Access DisplayTo make only the text on your screen larger adjust the slider under Make text biggerTo make everything larger including images and apps choose an option from the drop-down menu under Make everything bigger. This can range between a shrinkage rate of 4-15 depending on the properties of the clay and how it is fired. Reasons for process design 1 The design of the pouring system is unreasonable.
As a clay is fired higher it shrinks more and. Once the clay body now referred to as bisque-ware has been fired it is affected in various ways due to a chemical change in its mineral components and the removal of water including colour change shrinkage and increased strength. Shrinkage can even be used as an ally an example is slip casting the shrinkage pulls the piece away from the mold so it can be extracted.
The foam spheres produced from kaolin alone. If you dont see the formatting options menu at the bottom of the compose pane select Show. A glaze may now be applied to the bisque form using a variety of techniques and re fired.
It may cause shrinkage or porosity in the casting. Make the casting easy to produce shrinkage cavity or shrinkage porosity. Decrease of the porosity caused by the sintering process is determined by the level of the initial porosity of the green compact sintering temperature and time.
Air Drying Wet clay contains a large amount of water a minimum of 25 water. The change of shrinkage between 1400 and 1500 C was larger than others. Some of the particles shrink themselves kaolin is an example in the raw state particles are often loosely packed in layers these pull together at temperature rises.
How to Determine Clay Shrinkage and Make a Clay Shrinkage Ruler STEPHANI STEPHENSON. Heres how to change the size of text images and apps in Windows 10. Just about anything that is sintered firing clay will result in some loss of size due to shrink.
At the bottom of the compose pane select Font size. Clay does shrink when fired however different clay bodies do shrink at different rates. Fired shrinkage shrinkage from dry to fired is a thus comparative indicator of the degree of vitrification.
Yes they do and depending on the clay composition and water content can vary the shrink factor from 8 to 14. The clay manufacturer or distributor should have specs including clay shrinkage at the various firing temperatures. For the polymerization method the maximum C.
Total shrinkage will usually be about 8-12. This is due to diminished size of the particles as they approach fusion and to the closer arrangement of particles in their glassy matrix. Sintering firing of pure oxide ceramics require relatively long time and high temperature because the diffusion.
Researchers at Ohio State University have developed a new technique for creating near net-shaped ceramic parts for high-tech devices like fuel cells medical implants cellular phones gas or. When composing a message you can change the font size and format. I have written on the wall for my Daves Porcelain 12 shrinkage.
The majority of shrinkage occurs early in the drying process that is why softer-than-usual plastic bodies shrink so much more. Shrinkage happens at the vitrification stage. People first started making ceramics thousands of years ago pottery glass and brick are among the oldest human-invented materials and were still designing brand new ceramic materials todaythings like catalytic converters for todays cars and high-temperature superconductors for tomorrows computers.
The shrinkage of samples changed from 2286 to 2735 when the sintering temperature increased from 1400 to 1600 C. Shrinkage volume reduction - If the total shrinkage of clay is specified to be 11 it will yield a 30 reduction in volume cubic inches which is important to account for when making bowls or containers of any sort. These parameters provide unique tools to manipulate the architecture of freeze-cast materials at multiple length scales in a single processing step.
Select the font size you want to use. Abstract and Figures. The main manifestation is improper pouring position.
I wrote on the bisque s with colbalt and clear glazed over it -these are easy to make and you learn right away about your clay body. The firing shrinkage of a clay is usually about the same as the drying shrinkage. The conductance change CGairG10ppm NO2 was reduced with an increase in the operating temperature.
Besides the flaws may also be generated by insufficient amount of ceramic particles in the dispersion or the type of resin used. These are cone 10 bars. By contrast stoneware will shrink about 11-13 when fired between.
The freezing of concentrated colloidal suspensions is a complex physical process involving a large number of parameters. She also teaches mask making to children and adults. Theres quite a big difference.
Change font size when composing email. When clay starts to dry water evaporates from it. Sintering is enhanced if a liquid phase takes part in the process liquid phase sintering.
Answer 1 of 2. This also prevents ceramic from staining or tainting by food you are preparing Due to the very smooth surface germs are not keen to live on ceramic having no dimples scratches etc to hide in. These factors result in shrinkage of ware during firing.
ACKNOWLEDGEMENTS This study was supported by a grant from the Korea Healthcare technology RD Project Ministry for Health Welfare and Family Affairs Republic of Korea. An emulsion-based injection molding process has been reported for the preparation of ceramic foam spheres from kaolin and alumina. Create a new message or reply to a message.
Therefore in a shrinkage point of view it is important to make a presintered zirconia block with uniform density to obtain a uniform shrinkage of the zirconia block. The differential shrinkage upon sintering induced by evaporation of solvent in the polymer loaded ceramic slurry on the exposed surface may lead to the observed cracks and porosities. Types of ceramics.
Clay Shrinkage During Drying And Firing Preventing Defects
Tidak ada komentar